
Expanded Polystyrene in its broadest sense is a rigid cellular plastic which is found in a multitude of shapes and applications. However, in this publication we refer solely to a specific product belonging to the family of Polystyrenes: Molded EPS. So that you know exactly which material we are talking about, we are going to identify which material is and which material is not within this publication's field of study. Molded EPS is (the primary subject material of this publication) the material used for fish boxes, packaging for electric consumer goods and insulation panels for building. These are the most commonly known uses and as we'll see later there are many more... XPS (Extruded Polystyrene) is also a plastic foam based on polystyrene but differs from EPS in that it does not come out pearl-shaped but rather as a plank through a process of extrusion, using expansion gases which differ from those used for expanding EPS, like EPS it is normally used as thermal insulation in the construction industry and is usually colored (blue or pink). Extruded Polystyrene Trays also sometimes known as PSP (Polystyrene Paper) is an extruded Polystyrene foam in thin thickness sheet form (usually 2 or 3mm) then shaped by vacuum. This is the material used to manufacture the classic trays for wrapping small portions of foodstuffs and which we usually see at the supermarket.
Nonetheless, we now turn our attention away from XEPS and PSP since they are not the subject matter of this publication.
Raw Material Manufacturing: Expanded Polystyrene (foam) is obtained from expandable polystyrene (beads), which is a rigid cellular plastic which contains an expansion agent. Expandable polystyrene is therefore obtained from oil as can be seen from the diagram. 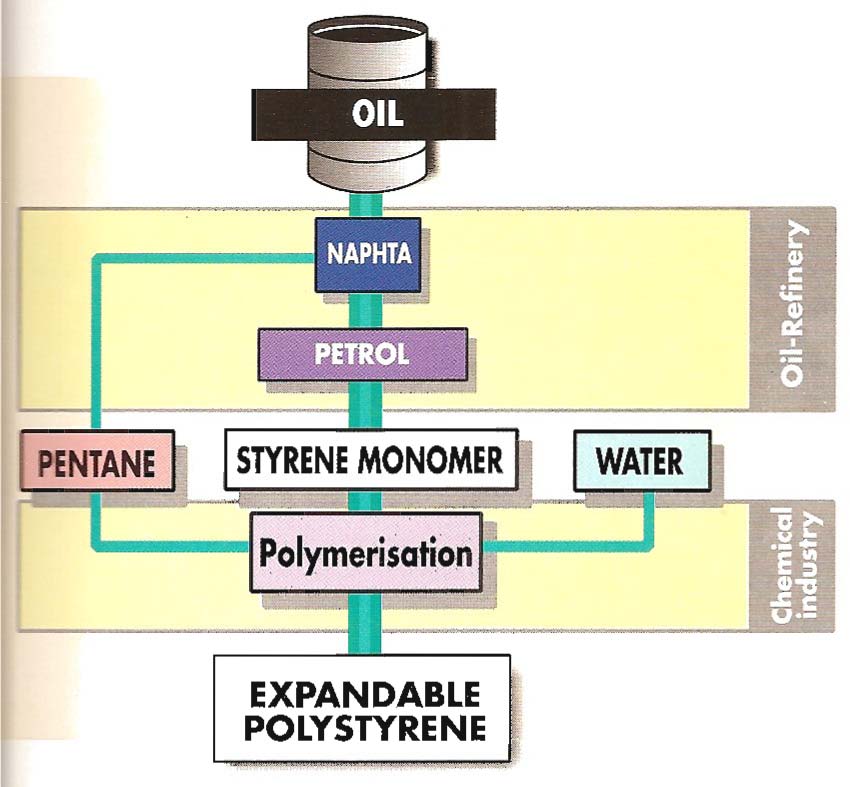 The EPS Manufacturing Process is inextricably linked with the process described in the last section, which brought us from the oil well to expandable polystyrene, now we will see what happens in the transformation process that leads us to Expanded Polystyrene foam parts. We have seen that the raw material is obtained through a chemical process. The next process involves the use of physics and the conversion process is carried out in three stages.
1st stage - PRE-EXPANSION: The raw material (beads) is heated in special machines called pre-expanders with steam at temperatures of approximately 215-f. The density of the material falls from 40lbs/cu ft to values of usually between 1 ~ 2lbs/cu ft. During the process of pre-expansion the raw material's hard beads turns into cellular (foam) plastic beads with small closed cells that hold air in their interior. 2nd stage - INTERMEDIATE MATURING AND STABILIZATION: On cooling, the recently expanded particles form a vacuum in their interior and this must be compensated for by air diffusion. This is how the beads achieve greater mechanical elasticity and improve expansion capacity, something very useful in the following transformation stage. This process is carried out during the material's intermediate maturing in aerated silos or mesh bags. The beads are dried at the same time. 3rd stage - EXPANSION AND FINAL MOLDING: During this stage the stabilized pre-expanded beads are transported to molds where they are again subjected to steam so that the beads bind together. In this way large blocks are obtained - "block molding" - (that are later sectioned to the required shape like boards, panels, cylinders etc.) or products in their final finished shape - "shape molding".
|